1. Silver Marks / Surface Streaks
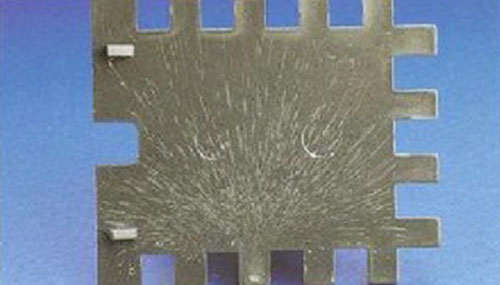
The process of injecting molten plastic into a mold is known as injection molding. The desired texture of the cavity steel is picked up by the molten plastic and imitated on the part. The temperature at which plastic melts varies depending on the base polymer being molded, from 176 °C to as high as 399 °C. Water turns to steam at these temperatures, and some low-molecular-weight additives may burn and produce volatiles. The speed at which the plastic is injected into the mold will shear the molecules as well. The molecules may deteriorate under excessive shear. The plastic then flows into the mold along with steam and volatiles (hereafter collectively referred to as volatiles) from degradation. The volatiles reach the surface and prevent the molten plastic from coming into contact with the mold steel while also spreading the volatile on the interface of the melt and the mold steel due to the fountain flow of the plastic into the mold cavities. This manifests as streaks and is referred to as splay. Splay is a different name for Silver streaks.
Silver stains degrade the mechanical strength of plastic components in addition to their appearance. The gases in the plastic part's melt surface are primarily to blame for the formation of the silver marks. We can learn how to address the flaws by identifying the source of these gases.
Sources of defect:
Material/ Granulate:
- Residual moisture in the granulate too high
- Packaging defect of the granulate
- Additives are moisture-sensitive (soot)
Plasticising:
- Back pressure too low
- Decompression path too big
- Gas content too high
- Dosing speed too low
- Dosing volume too low
- Melt temperature too low
- Pre-drying temperature too low / time too short
- Feed line/hoper part too cold
Cooling:
- Mould temperature too low (cold)
Injection:
- Injection speed too low
Mould:
- Mould leaking (cooling hole fissure)
- Flow cross-section too small
- Insufficient ventilation
Machine:
- Hopper is not covered
- No shut-off nozzle
- Dryer defect (in need of maintenance)
- Dryer too small
- Feed route for the material too long
- Use of 3- zone screw