1. Сребристи ивици/ пръски
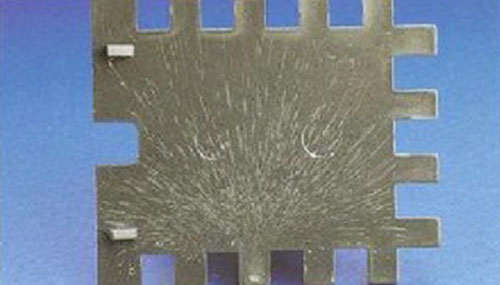
Процесът на шприцване на разтопена пластмаса във форма е известен, като леене под налягане, при което желаната текстура на активната стоманена кухина се имитира на детайла. Температурата, при която се топи пластмасата, варира в зависимост от основния полимер, който се формова до 399 °C. Водата се превръща в пара при тези температури и някои добавки с ниско молекулно тегло могат да изгорят и да произведат летливи вещества. Скоростта, с която пластмасата се инжектира във формата, също ще разкъса молекулите. Молекулите могат да се влошат при прекомерно накъсване. След това пластмасата се влива във формата заедно с парата и летливите вещества от разграждането. Летливите вещества достигат до повърхността и предотвратяват контакта на разтопената пластмаса със стоманената форма, като същевременно се разпространяват върху повърхността на стопилката и формата, поради фонтанния поток на пластмасата в кухините. Това се проявява, като сребърни ивици или пръски.
Сребърните ивици влошават механичната здравина на пластмасовите детайли в допълнение към външния им вид. Газовете в разтопената повърхност на пластмасовия детайл са основно причина за образуването на пръските.
Този недостатък може да се избегне, като се идентифицира източника на тези газове.
Източник на дефекта:
Материал/гранулат:
- Остатъчната влага в гранулата е твърде висока
- Дефект на опаковката на гранулата
- Добавките са чувствителни към влага (сажди)
Пластифициране:
- Обратното налягане е твърде ниско
- Пътят на декомпресия е твърде голям
- Твърде високо съдържание на газ
- Обемът на дозиране е твърде малък
- Температурата на стопилка е твърде ниска
- Температурата на предварително сушене е твърде ниска/ времето е твърде кратко
- Захранващият тръбопровод/входа на шнека е твърде студена
Охлаждане:
- Температурата на формата е твърде ниска (студено)
Шприцване:
- Скоростта на шприцване е твърде ниска
Форма:
- Теч във формата (пукнатина на охлаждащия отвор)
- Напречното сечение на потока е твърде малко
- Недостатъчна вентилация
Машина:
- Бункерът не е покрит
- Липса на затваряща дюза
- Проблем в сушилнята (има нужда от поддръжка)
- Сушилнята е твърде малка
- Пътят за подаване на материала е твърде дълъг
- Използване на шприц-машина с 3- зонов винт