1. Silberne Markierungen / Oberflächenschlieren
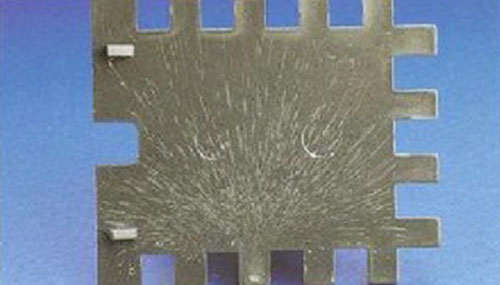
Das Verfahren, bei dem geschmolzener Kunststoff in eine Form gespritzt wird, nennt man Spritzgießen. Die gewünschte Textur des Hohlraumstahls wird von dem geschmolzenen Kunststoff aufgenommen und auf dem Teil nachgebildet. Die Temperatur, bei der der Kunststoff schmilzt, variiert je nach Basispolymer, das geformt wird, von 176 °C bis zu 399 °C. Bei diesen Temperaturen verwandelt sich Wasser in Dampf, und einige niedermolekulare Additive können verbrennen und flüchtige Stoffe erzeugen. Die Geschwindigkeit, mit der der Kunststoff in die Form gespritzt wird, schert die Moleküle ebenfalls. Die Moleküle können sich bei übermäßiger Scherung zersetzen. Der Kunststoff fließt dann zusammen mit Dampf und flüchtigen Bestandteilen (im Folgenden als flüchtige Bestandteile bezeichnet) aus dem Abbau in die Form. Die flüchtigen Stoffe gelangen an die Oberfläche und verhindern, dass der geschmolzene Kunststoff mit dem Formstahl in Berührung kommt, während sich die flüchtigen Stoffe durch das Einströmen des Kunststoffs in die Formhohlräume an der Grenzfläche zwischen der Schmelze und dem Formstahl verteilen. Dies äußert sich in Form von Schlieren und wird als Splay bezeichnet. Splay ist eine andere Bezeichnung für Silberschlieren.
Silberschlieren beeinträchtigen nicht nur das Aussehen, sondern auch die mechanische Festigkeit von Kunststoffteilen. Die Gase in der Schmelzoberfläche des Kunststoffteils sind in erster Linie für die Bildung der Silberschlieren verantwortlich. Wir können lernen, wie wir die Fehler beheben können, indem wir die Quelle dieser Gase identifizieren.
FEHLERQUELLEN:
Material/ Granulat
- Restfeuchte im Granulat zu hoch
- Verpackungsfehler des Granulats
- Zusatzstoffe sind feuchtigkeitsempfindlich (Russ)
Plastifizierung:
- Gegendruck zu niedrig
- Dekompressionspfad zu gross
- Gasgehalt zu hoch
- Dosierungsgeschwindigkeit zu niedrig
- Dosiermenge zu niedrig
- Schmelztemperatur zu niedrig
- Vortrocknungstemperatur zu niedrig / -Zeit zu kurz
- Zuführungsleitung / Operatorteil zu kalt
Kühlung:
- Temperatur der Spritzgussform zu niedrig (kalt)
Einspritzung:
- Einspritzgeschwindigkeit zu gering
Spritzgussform:
- Form undicht (Riss in der Kühlöffnung)
- Durchflussquerschnitt zu klein
- Unzureichende Lüftung
Maschine:
- Trichter ist nicht abgedeckt
- Keine Absperrdüse
- Trockner defekt (wartungspflichtig)
- Trockner zu klein
- Vorschubweg für das Material zu lang
- Verwendung der 3-Zonen Schraube