1. The cycle starts with- Closing the injection mould
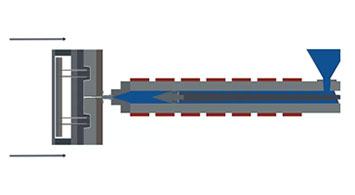
In the simplest application, the injection molding machine closes the mold and applies pressure. The force of this clamping is set by the operator and is measured in kN and depends on the profile of the part, the size of the mold and the capabilities of the machine. During this process, the machine monitors how much pressure it applies as a safety check. Also, a closing "profile" can be used where the operator sets different speeds as the mold closes. This profile setting is used more as shapes become more complex.
In more advanced applications, injection molds will have other actions, hydraulics, side systems, and developing operations that work in tandem with the mold closing operation. They can work outside of time, position, or mechanically with form. In general, it is important to find a balance between fast closing and safety. It's not worth pushing the machine to its limits to produce a few more details in this rush, but it certainly has its place in the industry.